Fräsen – Arbeitsplanung – Teil 6
Nun haben wir alle Vorbereitungen zur Abarbeitung unseres Programms getroffen. An dieser Stelle können wir nun das Programm simulieren.
Um Ihnen am Beispiel dieser Übungsaufgabe zu zeigen, wie wir mit der verwendeten Fräsmaschine in SinuTrain unsere programmierten Werkstücke simulieren können, starten Sie nun das Video:
Führen Sie nun die Simulation, wie in der Präsentation gelernt, selbstständig durch.
Na, hat alles geklappt? Wenn ja, müsste Ihnen folgendes Problem aufgefallen sein:

Abb. 4.27: Fräswerkstück Übung 16 mit Materialresten
Wir können die vorbearbeitete Kontur nicht im Rohteil darstellen. Deshalb wird die Bearbeitung über die ganze Schnitttiefe durchgeführt. Für unsere Übungsaufgabe ist dies aber nicht von Nachteil. Wir können somit sehr schnell erkennen, dass noch Materialreste an unserem Werkstück übrig geblieben sind. Diese müssen noch weg gefräst werden. Wir müssen also unser bereits programmiertes Programm noch einmal ergänzen. Lassen Sie uns diesen Vorgang gemeinsam erledigen. Wir steigen vor dem Punkt ein, an welchem wir auf den Werkzeugwechselpunkt fahren würden, also nach Abwahl der Werkzeugradiuskorrektur bei N320. Nachfolgend nochmals der entsprechende Programmabschnitt zum besseren Verständnis:
N320 G40
N330 WWP
N340 M30
Anstelle des Aufrufes unseres Programms für den Werkzeugwechselpunkt positionieren wir nun unser Werkzeug auf die erste Position, an der sich die Materialreste befinden. Betrachten wir diese Positionen anhand der technischen Zeichnung unseres Werkstückes etwas genauer.
Die Koordinaten zur Bestimmung von P1 befinden sich unter Berücksichtigung der Werkstücknullpunktlage bei X0 und Y-40. Für P2 befinden sich die Koordinaten bei X0 und Y40. Angefahren wird der Punkt von dem Koordinatenschnittpunkt von X70 Y-53 und Z-10. Wir entfernen die Materialreste ohne Benutzung von einer Werkzeugradiuskorrektur. Somit ergibt sich folgender Bearbeitungsablauf:

Abb. 4.28: Fräswerkstück Übung 16 Konturpunkte P1 und P2 der Bearbeitungsreste
Wir fahren im Eilgang in der Z-Achse auf einen Sicherheitsabstand von 2 mm über das Werkstück. N320 lautet somit:
N330 G0 Z2
Im nächsten Satz positionieren wir die X-Achse und die Y-Achse. Natürlich berücksichtigen wir wieder den Fräserradius von 8 mm und einen Sicherheitsabstand von 5 mm. Es ergibt sich für die X-Achse folgende Koordinate:
Wert von P1 in X + Fräserradius + Sicherheitsabstand = 0 mm + 8 mm + 5 mm = 13 mm
Wir positionieren den Fräser in X auf 13.
Allerdings müssen wir dies nur in der X-Achse berücksichtigen, da wir keine Fräserradiuskorrektur benutzen. Somit steht in der Y-Achse das Werkzeug mit dem Fräsermittelpunkt auf der programmierten Koordinate.
Wir programmieren für N340:
N340 G0 X13 Y-40
Nun stellen wir im Eilgang auf die Tiefe der Kontur. Anschließend fahren wir im Vorschub ins Werkstück. Ich programmiere in diesem Fall immer den Wert des Fräserradius bezogen auf den Werkstücknullpunkt. Wir fahren also in X auf -8 mm. Danach fahren wir im Eilgang wieder auf den Sicherheitsabstand von 2 mm über das Werkstück. Die nächsten Sätze lauten:
N350 G0 Z-10
N360 G1 X-8
N370 G0 Z2
Nun positionieren wir auf die Koordinaten von P2 nach gleicher Vorgehensweise. Die X-Koordinate zur Positionierung ist die gleiche wie bei P1 und die Y-Koordinate haben wir ebenfalls schon bei der Analyse bestimmt.
Wir programmieren:
N380 G0 X13 Y40
N390 G0 Z-15
N400 G1 X-8
Nun fahren wir wieder in der Z-Achse im Eilgang auf den Sicherheitsabstand von 2 mm über das Werkstück. Danach fahren wir in gewohnter Weise den Werkzeugwechselpunkt an und beenden das Programm mit M30.
N410 G0 Z2
N420 WWP
N430 M30
Das gesamte Programm von Übung 16 sieht ergänzt nun folgendermaßen aus:
N20 ; Übung_16
N30 ; 02.01.2013 Christiani Team
N40 ; G17 G54 G64 G90 G94
N50 G0 Z200
N60 WWP
N70; Anfertigen Absatz 20 mm x15 mm mit Schaftfräser Ø25 mm
N80 T=”SCHAFTFR_25″
N90 M6
N100 G97 S2037 F1222 M3 M8
N110 G0 X-117.5 Y-57.5
N120 G0 Z-15
N130 G41
N140 G1 X-100
N150 G1 Y57.5
N160 G40
N170 WWP
N180; Anfertigen Kontur Tiefe 10 mm mit Schaftfräser Ø16 mm
N190 T=”SCHAFTFR_16″
N200 M6
N210 G97 S3186 F1591 M3 M8
N220 G0 X-57 Y53
N230 G0 Z-10
N240 G41
N250 G1 X-70
N260 G1 Y39
N270 G3 X-61 Y30 CR=9
;N280 G1 X-14
;N290 G1 X-10 Y26
N280 G1 X-10 CHR=4
N290 G1 Y-30 CHR=4
N300 G1 X-70 RND=9
N310 G1 Y-53
N320 G40
N330 G0 Z2
N340 G0 X13 Y-40
N350 G0 Z-10
N360 G1 X-8
N370 G0 Z2
N380 G0 X13 Y40
N390 G0 Z-10
N400 G1 X-8
N410 G0 Z2
N420 WWP
N430 M30
Ergänzen Sie nun das Programm in Ihrem Programmeditor und simulieren Sie es erneut. Wenn Sie alles richtig gemacht haben, sollte das fertige Werkstück folgendermaßen aussehen:

Abb. 4.29: Fräswerkstück Übung 16 ohne Materialreste
Herzlichen Glückwunsch, das erste Fräswerkstück haben wir programmiert. Wieder haben Sie einen wichtigen Meilenstein in unserem Fernlehrgang gemeistert. Wir sind somit am Ende dieses Kapitels angekommen. Das Gelernte können Sie jetzt im Kapitel Prüfungsaufgaben vertiefen und überprüfen.
Nutzen Sie vorher die Zusammenfassung des Kapitel 5, um gut gerüstet zu sein für diese Aufgabe.
Zusammenfassung
Die Arbeitsplanung beim Fräsen findet nach folgenden Gesichtspunkten statt:
-
- die Spannung des Werkstückes
- die Auswahl der Werkzeuge
- die Planung der Arbeitsschritte
- die Bestimmung der Schnittdaten
- das Erstellen des Programms
- die grafische Simulation
- die Optimierung des Programms
-
Je nach Maschinentyp findet die Bearbeitung beim Fräsen in der Bearbeitungsebene G17, G18 oder G19 statt. Bei der Fräsmaschine, welche wir in diesem Fernlehrgang verwenden, arbeiten wir mit der Bearbeitungsebene G17.
Werkzeuge führen beim Fräsen ohne Anwendung der Werkzeugradiuskorrektur die Bearbeitung auf den Werkzeugmittelpunkt bezogen aus.
Beim Fräsen mit Werkzeugradiuskorrektur wird unterschieden in:
-
- G41 –> Gleichlauffräsen –> Werkzeug links der Fertigkontur
- G42 –> Gegenlauffräsen –> Werkzeug rechts der Fertigkontur
-

Abb. 4.30: Werkzeugradiuskorrektur beim Fräsen
Die Beurteilung, ob das Werkzeug links oder rechts der Kontur steht, erfolgt immer in Bezug von der Blickrichtung in Vorschubbewegung zu der Lage des Werkzeuges zur Fertigkontur.
Die wichtigsten Bezugspunkte beim Vermessen von Fräswerkzeugen sind die Punkte L, E und Q bzw. der Radius des Werkzeuges.
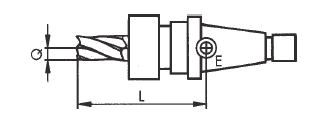
Abb. 4.31: Werkzeugkorrekturdaten bei Fräswerkzeugen
Das Vermessen der Werkzeuge erfolgt über Werkzeugvoreinstellgeräte.
Beim Fräsen wird mit konstanter Drehzahl gearbeitet. Dies geschieht mit der Angabe von G97 und dem errechneten Drehzahlwert S.
Beim Fräsen wird der Vorschub F mit der Vorschubgeschwindigkeit in mm/min Dies geschieht mit der G-Funktion G94.
Die Vorschubgeschwindigkeit wird nach folgender Formel berechnet:
Vf = n · fz · z
Vf = Vorschubgeschwindigkeit
n = Drehzahl
fz = Vorschub je Zahn
z = Anzahl der Zähne
Werkzeugaufruf erfolgt beim Fräsen entweder mit den Angaben der Werkzeugnummer und der Schneidennummer z. B. T1D1 (die Steuerung arbeitet mit Werkzeugkorrektur) oder mit dem T-Befehl und dem Werkzeugnamen z.B. T=„Schaftfr_25“ (die Steuerung arbeitet mit Werkzeugverwaltung). Wir programmieren in diesem Fernlehrgang die Möglichkeit mit Werkzeugverwaltung.
Bei Fräsmaschinen muss der Werkzeugwechsel mit dem M-Befehl M6 initialisiert werden.
Bei Fräsmaschinen müssen wir das Werkzeug mit einer Logik positionieren. Manche Steuerungen führen die Positionierlogik automatisch durch, das heißt, diese Maschinen positionieren beim Anfahren an des Werkstück zuerst die sogenannten Tischachsen und anschließend die Zustellachse. Beim Wegpositionieren vom Werkstück erfolgt das Positionieren der Achsen in umgekehrter Reihenfolge. Besitzt die Maschine keine Positionierlogik müssen wir dies beim Positionieren der Achsen selbst berücksichtigen und entsprechend programmieren.
Beim Positionieren von Werkzeugen beim Fräsen muss der Fräserradius und ein Sicherheitsabstand berücksichtigt werden.
Beim Ein- und Ausschalten der Werkzeugradiuskorrektur muss berücksichtigt werden, dass das Werkzeug eine Ausgleichsbewegung durchführt.
45°-Fasen können beim Fräsen mit dem Befehl CHF angefertigt werden.
Kreisinterpolationen werden nach gleicher Grundlage wie beim Drehen durchgeführt.
Anterior LektionSiguiente Lektion