Fräsen – Arbeitsplanung – Teil 2
Fräserarten
Die folgende Übersicht verschafft Ihnen einen kleinen Überblick, welche unterschiedlichen Fräserarten in der Frästechnik eingesetzt werden.

Abb. 4.7: Fräserarten
Fräserformen und Werkzeuge:
- Walzenfräser,
- Walzenstirnfräser,
- Walzenstirnfräser mit Spanteilern zum Schruppen,
- Scheibenfräser geradverzahnt,
- Scheibenfräser kreuzverzahnt,
- Metallkreissägeblatt,
- Winkelstirnfräser,
- Prismenfräser,
- Halbrundprofilfräser konvex,
- Halbrundprofilfräser konkav,
- Fräsmesserkopf,
- Langlochfräser gerade genutet,
- Langlochfräser drall genutet,
- Schaftfräser,
- Schaftfräser mit Spanteiler,
- Schaftfräser für T-Nuten,
- Gesenkfräser
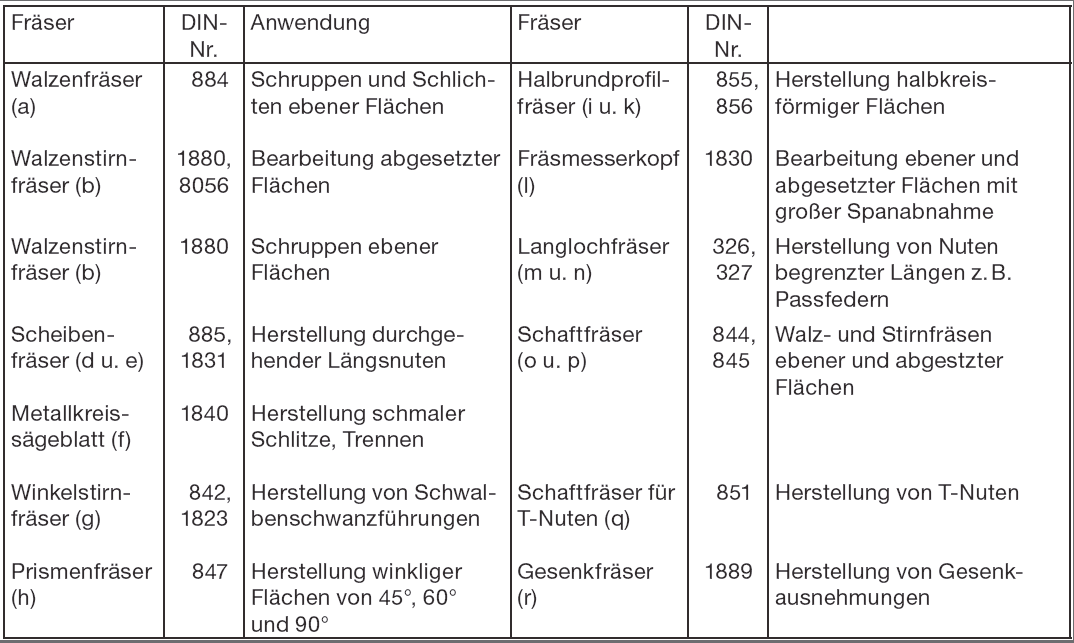
Abb. 4.8: Anwendungsfälle bestimmter Fräswerkzeuge
In der heutigen Zeit kommen in der CNC-Frästechnik fast ausschließlich Fräser aus Hartmetall (HM) oder Fräser, die mit Wendeschneidplatten bestückt sind, zum Einsatz. Alle Fräserarten, die in vorheriger Übersicht dargestellt sind, sind auch mit hartmetallbeschichteten Schneiden oder als Fräswerkzeug mit Wendeschneidplatten erhältlich.
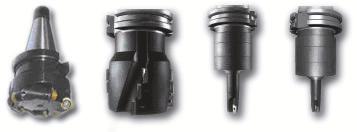
Abb. 4.9: Fräswerkzeuge mit Wendeschneidplatten und Werkzeugaufnahmen
Auch Bohrer verschiedenster Art sind wichtige Werkzeuge in der Frästechnik. Hier eine kleine Auswahl:
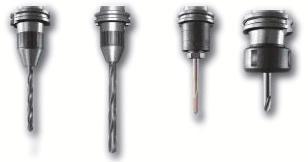
Abb. 4.10: Bohrwerkzeuge mit Werkzeugaufnahmen
Auf der Fräsmaschine ist immer eine Nullpunktverschiebung in allen drei Achsen notwendig. Die Verschiebungswerte, welche sich beim Aufspannen des Teiles ergeben, sind später im Nullpunktspeicher der CNC-Maschine unter der entsprechenden Nullpunktverschiebung (G54 bis G59) zu speichern. Da wir bei SinuTrain und der entsprechenden Fräsmaschine die Lage des Werkstückes nicht simulieren können, geben wir auf unserem Einrichteblatt die Lage des Nullpunktes und die Abmaße des Werkstückes an. Diese Werte setzten sich wie folgt zusammen:
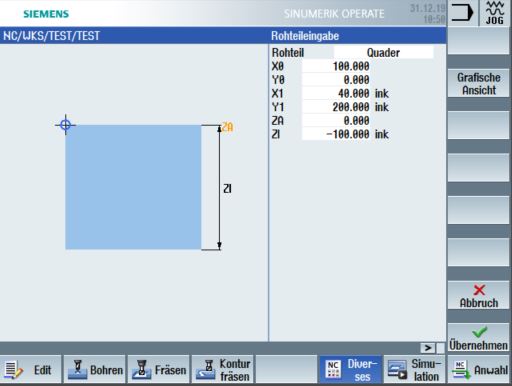
Abb. 4.11: Rohteilangabe und Bestimmung Werkstücknullpunkt mit SinuTrain
Eckpunkt 1 wird definiert mit unseren Achsen X, Y und Z. Hier geben wir diesen Eckpunkt in absoluter Form ein. Mit Eckpunkt 2, ebenfalls mit den Achsen X, Y und Z, bestimmen wir die Abmaße des Werkstückes. Diese ermittelten Werte tragen wir auf dem Einrichteblatt in den Spalten Definition Rohteil virtuelle Maschine ein. Wie diese Punkte ermittelt und in SinuTrain der entsprechenden Fräsmaschine eingetragen werden, zeige ich Ihnen später, wenn wir die Simulation durchführen. Die Maße für die Werkstücklänge, der Werkstückbreite und der Werkstückdicke ergeben sich aus den Rohteilangaben. Die Backenhöhe und die Unterlagenhöhe werden wir individuell, je nach Beschaffenheit der Konturen, die angefertigt werden, angeben. Somit hätten wir alle wichtigen Punkte des Einrichteblattes durchgesprochen.
Arbeitsplan Fräsen
Widmen wir uns nun dem Arbeitsplan. Der Arbeitsplan für die Frästechnik stellt fast keinen Unterschied zum Arbeitsplan der Drehtechnik dar. Nur die Angaben der Technologiewerte werden beim Fräsen in anderer Form angegeben. Während wir beim Drehen fast ausschließlich mit konstanter Schnittgeschwindigkeit gearbeitet haben, werden wir beim Fräsen vornehmlich mit konstanter Drehzahl G97 arbeiten. Auch der Vorschub wird beim Fräsen in einer anderen Einheit angegeben. Beim Drehen haben wir den Vorschub mit mm/U angegeben. In der Frästechnik arbeiten wir mit der Einheit m/min. Wie wir diese Werte aus den Tabellen heraus suchen, zeige ich Ihnen später, wenn wir die Arbeitsschritte genau planen. Folgenden Arbeitsplan verwenden wir in der Technologie Fräsen:
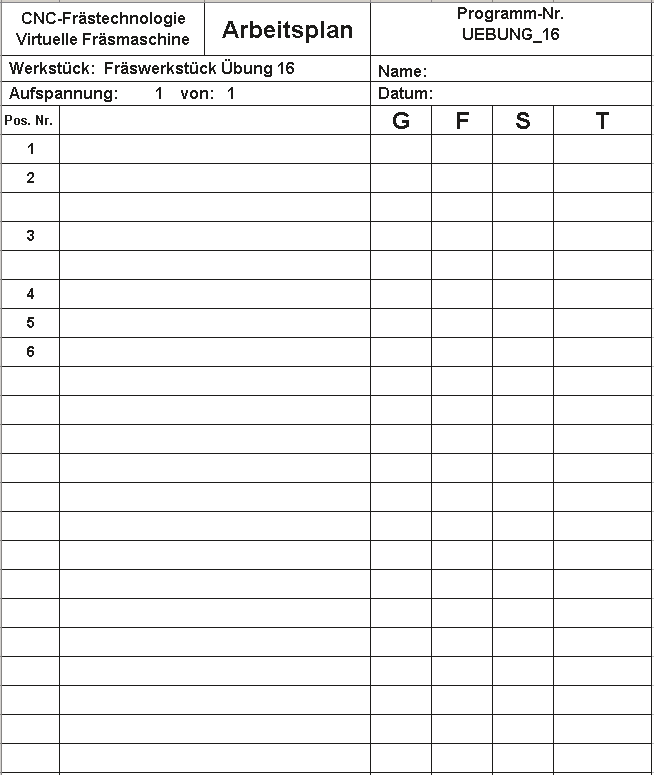
Abb. 4.12: Arbeitsplan Fräsen
Hier stellen wir Ihnen einen Arbeitsplan zum Ausfüllen zur Verfügung:
Nachdem Sie nun die Unterlagen zur Arbeitsplanung kennen gelernt haben, lassen Sie uns mit der Arbeitsplanung für unsere Übungsaufgabe beginnen.
Die Werkzeuge haben wir schon zu Beginn dieses Kapitels bestimmt. Dies sind die Schaftfräser Ø 25 mm und Ø 16 mm. Der Schaftfräser Ø 25 mm belegt Station 1 und der Schaftfräser Ø 16 mm belegt Station 2 im Werkzeugmagazin. Die Benennung der Fräser legen wir wie folgt fest:
- Für den Schaftfräser Ø 25 mm: SCHAFTFR_25
- Für den Schaftfräser Ø16 mm: SCHAFTFR_16
Beide Fräser sind aus Hartmetall und weisen eine Beschichtung mit TiCN (Titancarbonitrid) auf. Damit sind höhere Schnittgeschwindigkeiten und längere Standzeiten möglich. Die Werkzeuglängen, die wir eingeben, sind theoretische Werte, die ich festgelegt habe. Für beide Schaftfräser legen wir eine Länge von 125 mm fest. In der Praxis müssen wir hier die tatsächlich gemessenen Werte laut Werkzeugvoreinstellgerät eintragen. Der Fräser Ø 25 mm hat 6 Zähne, der Fräser Ø 16 mm verfügt über 5 Zähne. Diese Werte sind Erfahrungswerte.
Auch der Vorgang wie wir das Werkstück spannen muss wohl überlegt sein. Das Rohteil hat die Abmaße 120 × 80 × 25. Die Backenhöhe des Schraubstockes beträgt 30 mm. Die größte zu bearbeitende Tiefe ist 15 mm. Da die Werkstückdicke 25 mm misst, muss die Einspanntiefe kleiner als 10 mm sein. Eine Unterlagenhöhe von z. B. 22 mm ist hier richtig.
Dem Bereich der Definition Rohteil virtuelle Maschine kommt ein elementarer Stellenwert im Einrichtblatt zu. Wie bereits erwähnt, legen wir mit der Definition der Eckpunkte 1 und 2 das Rohteil sowie die Nullpunktlage des Werkstückes für unsere virtuelle Maschine fest. Das Werkstück besitzt eine symmetrische Kontur. Die Bemaßung geht überwiegend von der rechten Seite aus. Deswegen ist eine günstige Lage des Werkstücknullpunktes die Mitte der rechten Werkstückkante. Die Koordinaten des Werkstückes liegen damit in der X-Achse im negativen Bereich. In der Y-Achse bewegen wir uns im negativen und positiven Bereich. Wenn wir nun diese Überlegungen auf unser Werkstück übertragen, sieht die Lage des Werkstücknullpunktes folgendermaßen aus:
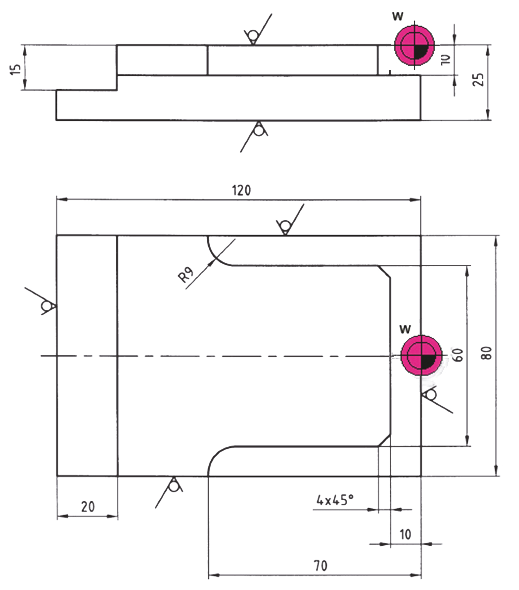
Abb. 4.13: Lage Werkstücknullpunkt Übung 16
Ermitteln wir nun die Maße für die Definition des Rohteiles in der virtuellen Maschine. Vergegenwärtigen wir uns noch einmal das Schema, welches wir bereits durchgesprochen haben, in der die Eckpunkte 1 und 2 erklärt sind.
Wie wir hier feststellen ist Punkt 1 an der vorderen oberen Ecke des Quaders. Wie bekomme ich nun den Eckpunkt 1 in die Mitte, wo sich auch der Werkstücknullpunkt befindet? Eigentlich ganz einfach. Da wir die Eckpunkte in absoluter Maßangabe angebe müssen, geben wir den Eckpunkt 1 in der Y-Achse in negativer Form an.
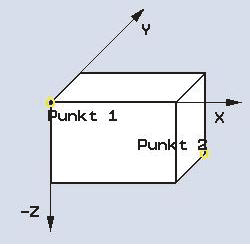
Abb. 4.14: Angabe der Eckpunkte des Rohteiles bei virtueller Fräsmaschine Übung 16
Auch hier beträgt der Wert die Hälfte der Rohteilbreite. Eckpunkt 1 ist in der X und Z-Achse jeweils auf dem Absoluten Wert 0. Der X Wert des Eckpunktes 2 spiegelt die Länge des Rohteiles wider. In unserem Beispiel 120. Die Dicke des Rohteiles wird in Der Z-Achse bei Eckpunkt 2 angegeben und zwar in negativer Form, also -25. Fassen wir noch einmal zusammen. Die Werte für unsere Eckpunkte für die Definition des Rohteiles in den virtuellen Maschinen lauten:
Ein fertig ausgefülltes Einrichteblatt zu dieser Übungsaufgabe als Lösungsvorschlag können Sie sich hier ansehen. (Klicken zum vergrößern):
Befassen wir uns jetzt mit dem Arbeitsplan zu dieser Übungsaufgabe.
Bei Pos. 1 und Pos. 2 tauchen die Standardschritte, die wir bereits aus der Drehtechnik kennen, auch hier beim Fräsen auf. Bei Pos. 1 kontrollieren wir die Rohmaße des Rohteils und entgraten das Werkstück. Bei Pos. 2 wird das Werkstück nach Einspannskizze gespannt. Anschließend wird bei Pos. 3 der Absatz Tiefe 15 mm, Breite 20 mm angefertigt. Auch hier müssen wir die Schnittgeschwindigkeit für unser Werkzeug ermitteln. Zusätzlich muss beim Fräsen noch der Vorschub je Zahn ermittelt werden. Diese Daten erhalten wir aus folgender Tabelle:
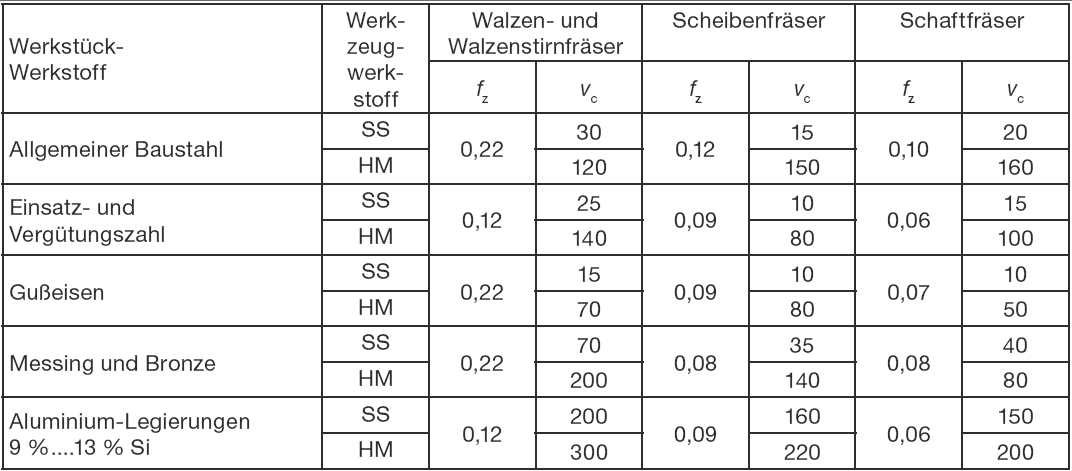
Abb. 4.15: Tabelle Technologiedaten Fräsen
Wir ermitteln folgende Werte:
Wir bearbeiten S235JR (allgemeiner Baustahl). Der Schneidstoff des Schaftfräsers (Werkzeug Werkstoff) ist Hartmetall (HM). Aus der Tabelle ergeben sich für die Schnittgeschwindigkeit der Wert Vc = 160 m/min und der Wert für den Vorschub je Zahn von fz = 1 mm/Zahn.
Anders als beim Drehen, wird in der Fräsbearbeitung nicht die Schnittgeschwindigkeit, sondern die Drehzahl programmiert. Für den Einsatzzeitraum eines Werkzeugs bleibt der Bezugsdurchmesser (hier der Fräser-Ø) d immer gleich. So besteht nicht die Notwendigkeit einer ständigen Drehzahlanpassung. Allerdings ist die Drehzahl zu ermitteln. Die Formel zur Drehzahlermittlung sei zur Erinnerung hier noch einmal aufgeführt:
Wenn wir hier die Werte für Vc (160 m/min) und d (Ø 25 mm) einsetzen und die Drehzahl berechnen, erhalten wir für die Umdrehung folgenden Wert:
Die Wegbedingung G97 ordnet der Adresse S die Drehzahl zu. Eine weitere Berechnung ist für die Bestimmung des zu programmierenden Vorschubes erforderlich. Die Maschinen verlangen die Vorschubgeschwindigkeit in mm/min.
Diese Geschwindigkeit errechnet sich nach dieser Formel:
Vf = n · fz · z
Die Zähnezahl des Fräsers ist im Einrichteblatt eingetragen und beträgt 6. Die Berechnung lautet also:
Vf = 2037 U/min × 0,1 mm /Zahn × 6
Vf = 1222 mm/min
Fassen wir an dieser Stelle Pos. 3 zusammen.
Tragen sie Folgendes im Arbeitsplan ein:
Anfertigen Absatz 20 mm × 15 mm mit Schaftfräser Ø 25 mm; Vc = 160 m/min; fz = 0.1 mm/Zahn
G97; F1222; S2037; T=„SCHAFTFR_25“
Fahren wir nun mit Pos. 4 fort. Wir fertigen die Kontur mit der Tiefe 10 mm an. Diese Bearbeitung wird mit dem Schaftfräser Ø 16 mm durchgeführt. Die Schnittgeschwindigkeit Vc und der Wert für fz bleiben gleich. Nur die Zähnezahl und der Durchmesser des Schaftfräsers ändert sich. Führen Sie die Berechnung für die Drehzahl n und die Vorschubgeschwindigkeit Vf selbstständig durch. Wenn Sie alles richtig berechnet haben, müssten Sie folgende Werte errechnet haben:
n ~ 3183 U/min; Vf = 1591 mm/min.
Anfertigen Kontur Tiefe 10 mm mit Schaftfräser Ø 16 mm; Vc=160 m/min; fz = 0.1 mm/Zahn
G97; F1591; S3183; T=„SCHAFTFR_16“
Unter Pos. 5 spannen wir das Werkstück aus. Anschließend entgraten wir das Werkstück und führen die Qualitätskontrolle unter Pos. 6 durch. Übertragen Sie diese Daten nun in das Formular Arbeitsplan.
Einen fertig ausgefüllten Arbeitsplan sowie das Einrichteblatt Sie sich hier ansehen. (Klicken zum vergrößern):
Die Tabelle zur Ermittlung der Technologiewerte finden Sie in Abb. 4.15.
Vorherige LektionNächste Lektion